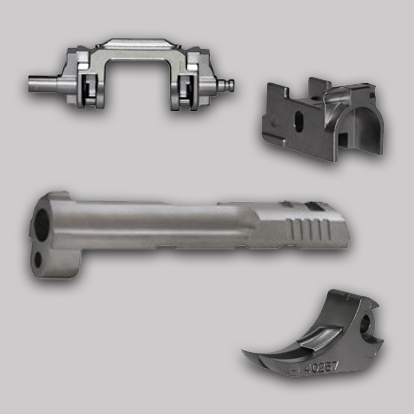
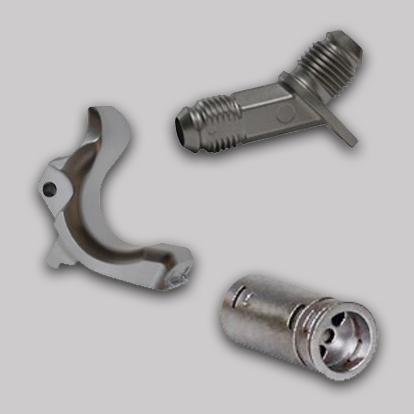
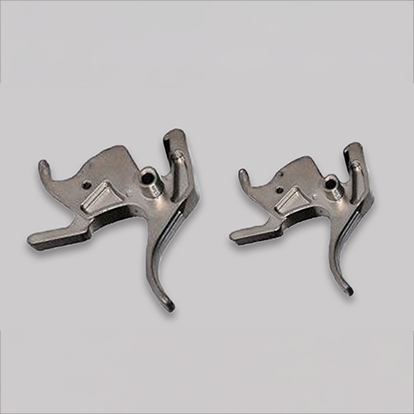
MIM (Metal Injection Molding)
The MIM (Metal Injection Molding) process was developed in the early ’90s in the United States, mainly for use in the military sector. In the following years, MIM usage and design capabilities have grown greatly. This is due to interest shown by a growing number of industries where parts made by the MIM process can be used. These industries include but are not limited to Automotive, Medical, Firearms/Military, Cutlery, Hand tools, Power tools, Optics, and Electronics.
The advantage of the MIM process is making average to small pieces with a complex shape or three-dimensional shapes in medium to high volume quantities of very high strength. These parts are made in high strength ferrous materials. Automation is heavily used in the MIM process to maintain high repeatability and high-quality parts. The molding process is very much like plastic injection with the machines and tools very similar in design and function.
The Malleability of Plastic, The Tenacity of Steel
MimEcri USA offers wide possibilities to many present industries in steels and other alloys, competing advantageously in quality and price with other traditional manufacturing processes. This is made possible thanks to our design characteristics and finishing with tight tolerances and machining savings. With more than 200 production people, Ecrimesa combines youth and experience to provide a dynamic and modern Company. Service to customers and environmental protection are very important parts of the management philosophy. To meet these requirements Ecrimesa is equipped with the most advanced and modern production facilities in M.I.M technology in the world. With every day higher a level of exigency required to produce, Mimecrisa offers it’s customers wide possibilities by its Metal Injection Molding technique (M.I.M.). Belonging to the Ecrimesa Group, MimEcrisa is one of the leading companies worldwide in the development and manufacturing of M.I.M. technology. Mimecrisa began its activity in 1991 and more than a hundred new parts per year have been developed since then. Being a supplier to customers in 22 countries in the industrially-developed world. More than 60% of our company production is supplied to the automotive and firearms industry. Production capacity is higher than 200 Tm/year with a highly qualified technical staff and technology equipment.
Secondary Operations
Like wrought material components, MIM parts can have any secondary operations that need to be carried out. These include: